Exchange solution for tilting angle monitoring
- Direct mounting / elimination distribution gear
- Higher accuracy
- Easy configuration of switching points
- Fast commissioning and restart after preset
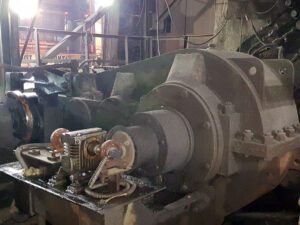
Before: Mechanical cam limit switch and absolute encoder mounted by using an additional distribution gear.
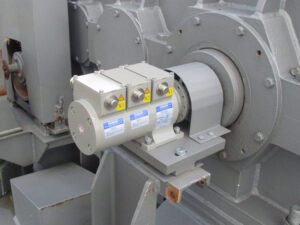
After: Electronic position switches and absolute encoder in one unit directly mounted without distribution gear.
In steel making plants tilting angles of converters are measured by absolute encoders and monitored by mechanical cam limit switches.
The sensors are normally mounted by using an additional distribution gear, which causes mechanical play and inaccuracy. Furthermore, the mechanical cam limit switches are difficult to preset and not precise enough.
The universal encoder system U-ONE-(SAFETY-) Compact provides the same outputs as the old solution, but in just one compact and robust unit:
- Absolute encoder
- Electronic position switches
The unit can be mounted directly to the application shaft without using any distribution gear. For this Hübner Giessen provides special torsion resistant double-joint couplings. The switching points are easy to configure and the system can be restarted fastly after preset.
Optionally available with safety certification SIL 2 / PL d.